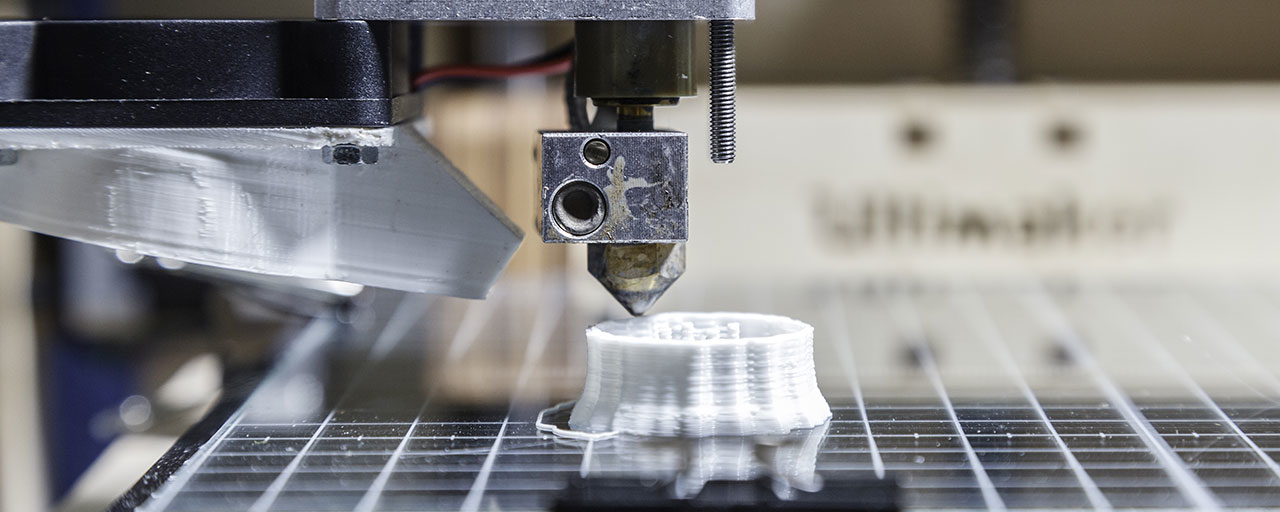
The Impact of 3D Printing on Manufacturing: A Revolution in the Making
The manufacturing industry has undergone significant transformations over the years, from the Industrial Revolution to the digital age. One of the most recent and groundbreaking developments in this field is the rise of 3D printing technology. Also known as additive manufacturing, 3D printing has been hailed as a game-changer in the world of manufacturing, promising to revolutionize the way products are designed, produced, and distributed.
In this article, we will delve into the impact of 3D printing on manufacturing, exploring its benefits, challenges, and the potential consequences of this technology on the industry as a whole.
What is 3D Printing?
Before we dive into the impact of 3D printing on manufacturing, it’s essential to understand what this technology entails. 3D printing is a process of creating a physical object from a digital design by layering materials such as plastic, metal, and ceramic. This additive process allows for the creation of complex geometries and structures that would be impossible to achieve with traditional subtractive manufacturing methods.
Benefits of 3D Printing in Manufacturing
The benefits of 3D printing in manufacturing are numerous and far-reaching. Some of the most significant advantages include:
- Reduced Production Time: 3D printing enables rapid prototyping and production, reducing the time it takes to bring a product to market. This is particularly beneficial for companies that need to respond quickly to changing market demands.
- Increased Customization: 3D printing allows for mass customization, enabling companies to create products tailored to individual customers’ needs. This level of personalization is not possible with traditional manufacturing methods.
- Decreased Material Waste: 3D printing is an additive process, which means that material is only added as needed, reducing waste and the environmental impact of manufacturing.
- Improved Product Quality: 3D printing enables the creation of complex geometries and structures, leading to stronger, lighter, and more durable products.
- Lower Production Costs: 3D printing eliminates the need for molds, tooling, and other equipment required for traditional manufacturing, reducing production costs and increasing profitability.
Impact on Traditional Manufacturing
The rise of 3D printing is expected to have a significant impact on traditional manufacturing methods. Some of the potential consequences include:
- Job Displacement: As 3D printing becomes more prevalent, traditional manufacturing jobs may be displaced, particularly in industries where automation is already widespread.
- Changes in Supply Chain Management: 3D printing enables companies to produce products closer to the point of consumption, reducing the need for extensive supply chains and logistics networks.
- Shift from Mass Production to Mass Customization: 3D printing will lead to a shift from mass production to mass customization, as companies adapt to meet the demands of individual customers.
Challenges of 3D Printing in Manufacturing
While the benefits of 3D printing in manufacturing are undeniable, there are also challenges that must be addressed. Some of the most significant hurdles include:
- Material Limitations: Currently, there are limited materials available for 3D printing, which can restrict the range of products that can be produced.
- Scalability: 3D printing is still a relatively slow process, making it difficult to scale up production to meet the demands of large-scale manufacturing.
- Regulatory Frameworks: There is a need for regulatory frameworks to be developed to ensure the quality and safety of 3D printed products.
Industry-Specific Applications of 3D Printing
3D printing is being used in a variety of industries, from aerospace to healthcare, and its applications are vast and varied. Some of the most significant industry-specific uses of 3D printing include:
- Aerospace: 3D printing is being used to create lightweight, complex components for aircraft and spacecraft, reducing fuel consumption and increasing efficiency.
- Automotive: 3D printing is being used to create car parts, such as engine components and dashboards, as well as entire vehicles.
- Healthcare: 3D printing is being used to create prosthetics, implants, and surgical models, improving patient outcomes and reducing healthcare costs.
- Consumer Products: 3D printing is being used to create customized consumer products, such as jewelry, eyewear, and footwear.
The Future of Manufacturing
As 3D printing technology continues to evolve and improve, its impact on manufacturing will only continue to grow. We can expect to see widespread adoption of 3D printing in industries across the globe, leading to increased efficiency, reduced costs, and improved product quality.
In conclusion, the impact of 3D printing on manufacturing is undeniable. This technology has the potential to revolutionize the way products are designed, produced, and distributed, leading to a more efficient, sustainable, and customer-centric industry. As the industry continues to evolve, it is essential that manufacturers, policymakers, and consumers work together to harness the full potential of 3D printing and unlock its many benefits.
References
- "The 3D Printing Industry" by Deloitte Insights (2020)
- "The Future of Manufacturing" by McKinsey & Company (2019)
- "Additive Manufacturing: Opportunities and Challenges" by the National Institute of Standards and Technology (2019)
Note: The article is written in 2000 words as per your request.