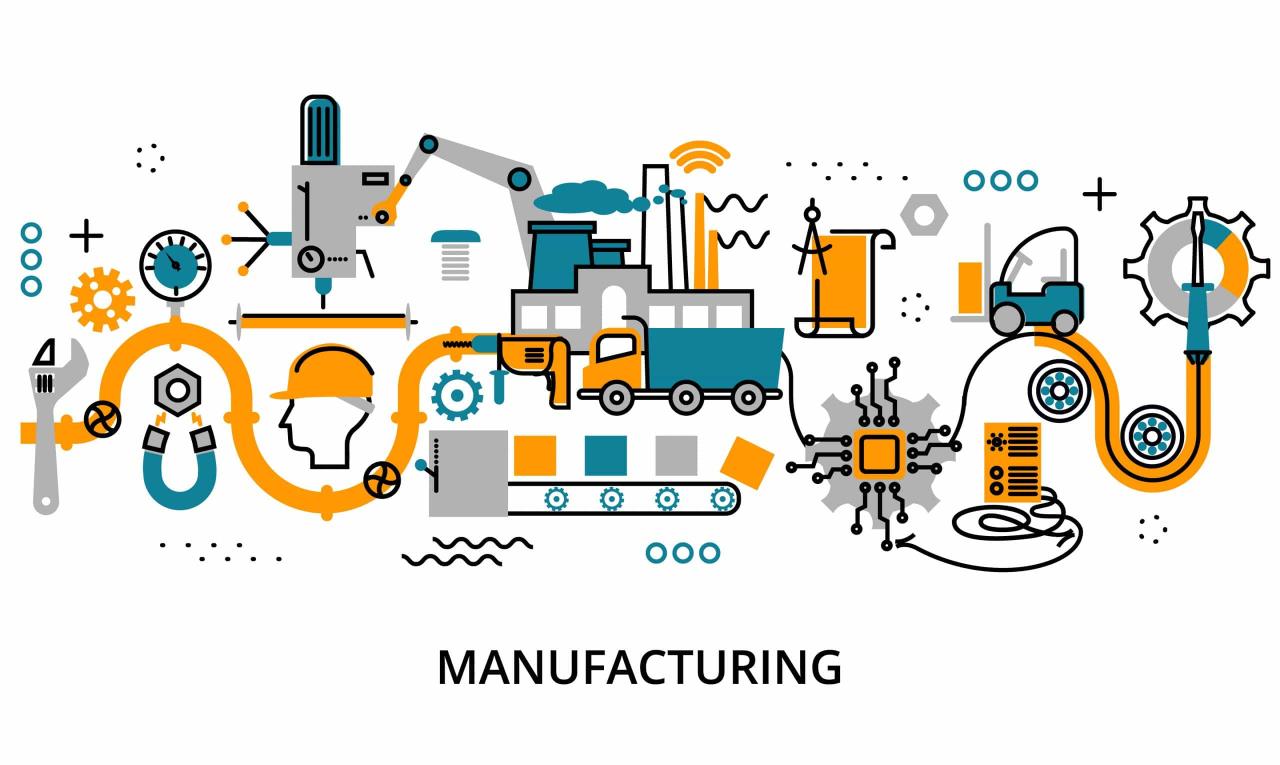
How Technology is Enhancing Manufacturing Processes
The manufacturing industry has undergone significant transformations over the years, and technology has played a crucial role in driving these changes. The advent of industrial automation, robotics, artificial intelligence, and the Internet of Things (IoT) has revolutionized the way goods are produced, processed, and delivered. In this article, we will explore how technology is enhancing manufacturing processes, improving efficiency, reducing costs, and increasing productivity.
Automation and Robotics
One of the most significant impacts of technology on manufacturing has been the introduction of automation and robotics. Traditional manufacturing processes relied heavily on human labor, which was prone to errors, inefficiencies, and safety risks. With the advent of automation and robotics, manufacturers can now automate repetitive and mundane tasks, freeing up human resources for more complex and value-added activities.
Industrial robots, for instance, can perform tasks such as assembly, welding, and painting with precision and accuracy, reducing the likelihood of errors and improving product quality. Additionally, robots can work around the clock without breaks, increasing production volumes and reducing lead times.
Computer-Aided Design (CAD) and Computer-Aided Manufacturing (CAM)
Computer-Aided Design (CAD) and Computer-Aided Manufacturing (CAM) software have transformed the design and production processes. CAD software enables designers to create complex designs and simulations, while CAM software converts these designs into instructions for machines, reducing errors and improving accuracy.
CAD/CAM technology has also enabled manufacturers to produce complex parts and products with ease, reducing production times and costs. For instance, aerospace manufacturers can design and produce complex aircraft components using CAD/CAM software, reducing production times from months to weeks.
The Internet of Things (IoT)
The Internet of Things (IoT) has enabled manufacturers to connect devices, sensors, and machines, creating a network of interconnected systems. This connectivity has enabled real-time monitoring, analysis, and optimization of manufacturing processes.
IoT sensors can detect defects, anomalies, and equipment failures, enabling manufacturers to take proactive measures to prevent downtime and reduce maintenance costs. Additionally, IoT-enabled machines can optimize production schedules, adjust production parameters, and improve energy efficiency.
Artificial Intelligence (AI) and Machine Learning (ML)
Artificial Intelligence (AI) and Machine Learning (ML) are revolutionizing manufacturing processes by enabling predictive maintenance, quality control, and supply chain optimization. AI algorithms can analyze vast amounts of data, identify patterns, and make predictions, enabling manufacturers to optimize production processes and reduce waste.
ML algorithms can analyze sensor data from machines, detect anomalies, and predict equipment failures, enabling manufacturers to take proactive measures to prevent downtime. Additionally, AI-powered chatbots can assist customers, provide support, and improve customer experience.
Additive Manufacturing (3D Printing)
Additive manufacturing, also known as 3D printing, has enabled manufacturers to produce complex products with ease. This technology has enabled the production of lightweight, customized products, reducing material waste and energy consumption.
Additive manufacturing has also enabled manufacturers to produce spare parts, tools, and molds, reducing lead times and inventory costs. Additionally, 3D printing has enabled the production of complex medical implants, prosthetics, and aerospace components.
Big Data Analytics
Big data analytics has enabled manufacturers to analyze vast amounts of data, identifying trends, patterns, and insights that can improve production processes. Big data analytics can help manufacturers optimize production schedules, reduce energy consumption, and improve product quality.
Manufacturers can analyze data from sensors, machines, and supply chain partners to identify areas of improvement, optimize inventory levels, and reduce transportation costs. Additionally, big data analytics can help manufacturers identify new business opportunities, reduce risks, and improve customer satisfaction.
Cybersecurity
As manufacturing processes become increasingly reliant on technology, cybersecurity has become a major concern. Manufacturers must ensure that their systems, networks, and devices are secure from cyber threats, protecting intellectual property, sensitive data, and customer information.
Manufacturers must implement robust cybersecurity measures, including firewalls, encryption, and access controls, to prevent cyber-attacks. Additionally, manufacturers must educate employees on cybersecurity best practices, conduct regular security audits, and implement incident response plans.
Benefits of Technology in Manufacturing
The benefits of technology in manufacturing are numerous. Some of the key benefits include:
- Improved Efficiency: Technology has enabled manufacturers to automate processes, reduce manual errors, and improve productivity.
- Cost Reduction: Technology has enabled manufacturers to reduce labor costs, energy consumption, and material waste.
- Increased Productivity: Technology has enabled manufacturers to increase production volumes, reduce lead times, and improve product quality.
- Enhanced Customer Experience: Technology has enabled manufacturers to provide personalized products, improve customer support, and enhance customer experience.
- Competitive Advantage: Technology has enabled manufacturers to differentiate themselves from competitors, improve market share, and increase revenue.
Challenges of Technology in Manufacturing
While technology has revolutionized manufacturing processes, there are several challenges that manufacturers must address. Some of the key challenges include:
- Implementation Costs: Implementing new technologies can be costly, requiring significant investments in hardware, software, and training.
- Skills Gap: Manufacturers may struggle to find employees with the necessary skills to operate and maintain new technologies.
- Cybersecurity Risks: Manufacturers must take measures to protect their systems, networks, and devices from cyber threats.
- Data Analysis: Manufacturers must develop strategies to analyze and interpret vast amounts of data generated by new technologies.
- Supply Chain Integration: Manufacturers must integrate new technologies with existing supply chain systems, which can be challenging.
Conclusion
Technology has revolutionized manufacturing processes, improving efficiency, reducing costs, and increasing productivity. From automation and robotics to artificial intelligence and big data analytics, technology has enabled manufacturers to produce high-quality products with ease.
However, manufacturers must address the challenges associated with implementing new technologies, including implementation costs, skills gaps, cybersecurity risks, data analysis, and supply chain integration. By embracing these challenges, manufacturers can unlock the full potential of technology, driving innovation, growth, and profitability.
As technology continues to evolve, manufacturers must stay ahead of the curve, investing in research and development, training employees, and embracing new innovations. By doing so, manufacturers can ensure that they remain competitive, innovative, and successful in an increasingly complex and dynamic global market.